More About Alcast Company
More About Alcast Company
Blog Article
An Unbiased View of Alcast Company
Table of ContentsLittle Known Facts About Alcast Company.Things about Alcast CompanyThe Basic Principles Of Alcast Company The 4-Minute Rule for Alcast CompanyThe Best Guide To Alcast CompanyThe 30-Second Trick For Alcast Company
Chemical Comparison of Cast Light weight aluminum Alloys Silicon advertises castability by minimizing the alloy's melting temperature and enhancing fluidity during spreading. In addition, silicon adds to the alloy's toughness and wear resistance, making it useful in applications where durability is important, such as vehicle parts and engine components.It also enhances the machinability of the alloy, making it less complicated to refine into finished items. In this means, iron adds to the total workability of light weight aluminum alloys. Copper boosts electrical conductivity, making it beneficial in electrical applications. It also boosts deterioration resistance and includes in the alloy's overall stamina.
Manganese contributes to the toughness of light weight aluminum alloys and boosts workability. Magnesium is a lightweight component that offers stamina and impact resistance to light weight aluminum alloys.
The Ultimate Guide To Alcast Company
It allows the production of lightweight parts with outstanding mechanical homes. Zinc improves the castability of aluminum alloys and helps regulate the solidification procedure during casting. It boosts the alloy's stamina and solidity. It is frequently found in applications where intricate shapes and fine details are essential, such as decorative castings and certain automobile parts.
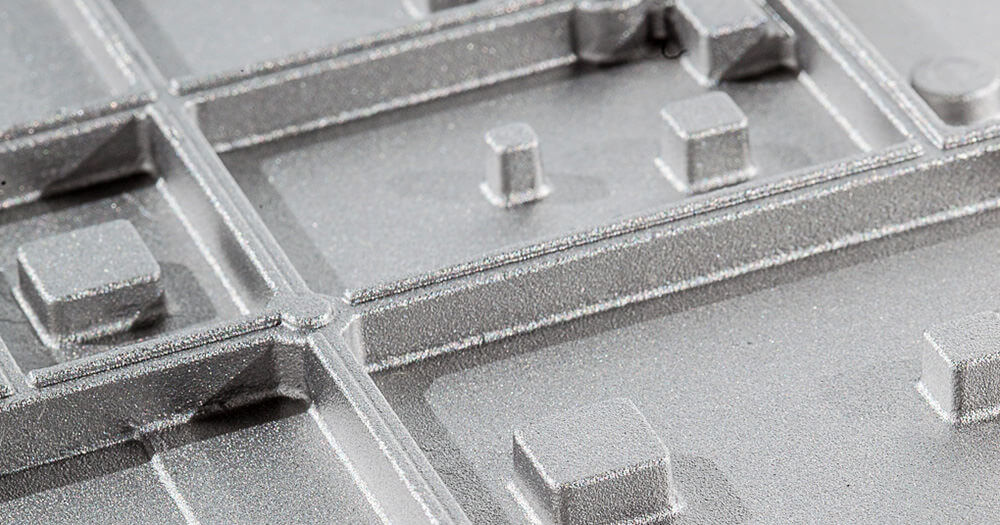
The key thermal conductivity, tensile toughness, return stamina, and elongation vary. Select appropriate basic materials according to the efficiency of the target item generated. Amongst the above alloys, A356 has the greatest thermal conductivity, and A380 and ADC12 have the least expensive. The tensile limitation is the contrary. A360 has the best yield strength and the greatest prolongation price.
Alcast Company Can Be Fun For Everyone

Its unique homes make A360 a beneficial choice for accuracy spreading in these sectors, enhancing product toughness and top quality. Light weight aluminum alloy 380, or A380, is an extensively made use of spreading alloy with several distinct characteristics. It supplies exceptional castability, making it a perfect choice for accuracy spreading. A380 displays excellent fluidness when molten, ensuring detailed and thorough molds are accurately reproduced.
In precision casting, light weight aluminum 413 shines in the Customer Electronic Devices and Power Equipment discover this industries. It's generally utilized to craft elaborate components like smartphone housings, camera bodies, and power device casings. Its accuracy is remarkable, with limited resistances approximately 0.01 mm, making sure perfect product assembly. This alloy's exceptional corrosion resistance makes it an outstanding selection for outdoor applications, guaranteeing durable, sturdy items in the discussed sectors.
The Facts About Alcast Company Uncovered
The aluminum alloy you choose will significantly impact both the casting procedure and the properties of the final product. Because of this, you need to make your decision thoroughly and take an informed approach.
Establishing one of the most suitable light weight aluminum alloy for your application will mean evaluating a wide selection of qualities. These relative alloy features follow the North American Die Spreading Organization's standards, and we've separated them right into 2 groups. The initial group addresses alloy features that influence the manufacturing process. The second covers qualities influencing the properties of the final item.
Getting My Alcast Company To Work
The alloy you choose for die casting straight impacts numerous aspects of the casting procedure, like exactly how easy the alloy is to collaborate with and if it is susceptible to casting defects. Hot fracturing, likewise referred to as solidification cracking, is a regular die spreading problem for light weight aluminum alloys that can lead to internal or surface-level splits or cracks.
Specific light weight aluminum alloys are much more susceptible to warm fracturing than others, and your option must consider this. Another common issue found in the die spreading of aluminum is die soldering, which is when the cast adheres to the die walls and makes ejection challenging. It can harm both the actors and the die, so you must try to find alloys with high anti-soldering residential properties.
Rust resistance, which is already a noteworthy characteristic of aluminum, can vary considerably from alloy to alloy and is a vital characteristic to think about depending on the environmental problems your item will be exposed to (Aluminum Casting). Put on resistance is another residential property frequently sought in light weight aluminum items and can differentiate some alloys
Report this page